You may be glad to hear that you know this quality tool – and might’ve even used it before without realizing it. The cheek sheet is yet another one of those quality tools that is easy, and intuitive to use but can make a huge difference. The main idea of this tool is to have a well-structured form for collecting and analyzing data. It is most often used to collect real-time data (both quantitative and qualitative) at the origin point or that point where this data is generated. Think production process anytime a defect is detected.
By now I think you might have a vague clue as to why that would be relevant but let’s make sure anyway. If we can collect data from a process, we can then analyze it and try to make sense of it, as in try to detect a pattern or a trend (and it might also come in handy when we want to get a quality management system certification due to the traceability it offers – but we’ll talk about that some more later on)
While there is not a specific pattern to be used and the tool, pretty much like the other quality tools is meant to be adapted to your needs, there are some recommendations from the ASQ (American Society of Quality) for the procedure as it follows:
- Deciding on the event or problem that will be observed, the type of data that wants to be collected, and the period assigned for it
- Designing the form so that data can be recorded simply by making check marks or x’s
- Labeling all the spaces on the form
- Testing the check sheet to ensure that it collects the appropriate data and is easy to use.
One of the most common uses of this tool in quality management is the quick registration of defects. So let’s jump to that for an example.
Let’s assume that we are interested in the defects related to the processing process of the tea leaves and so we are looking for an easy and quick way for our employees to register the type of defect that they encounter when checking the tea leaves.
We know from previous experience that the most common defects that are encountered in the process are: „Mold growth on tea leaves”, „Leaf spoilage”, „Dust/dirt on leaves” and „Chemical leftovers on leaves”. We will then create a simple table with these types of defects and the work days. Then, we’ll ask the employees to mark a line every time they find a specific type of defect with the tea leaves in the cell of the day when the defect was found.
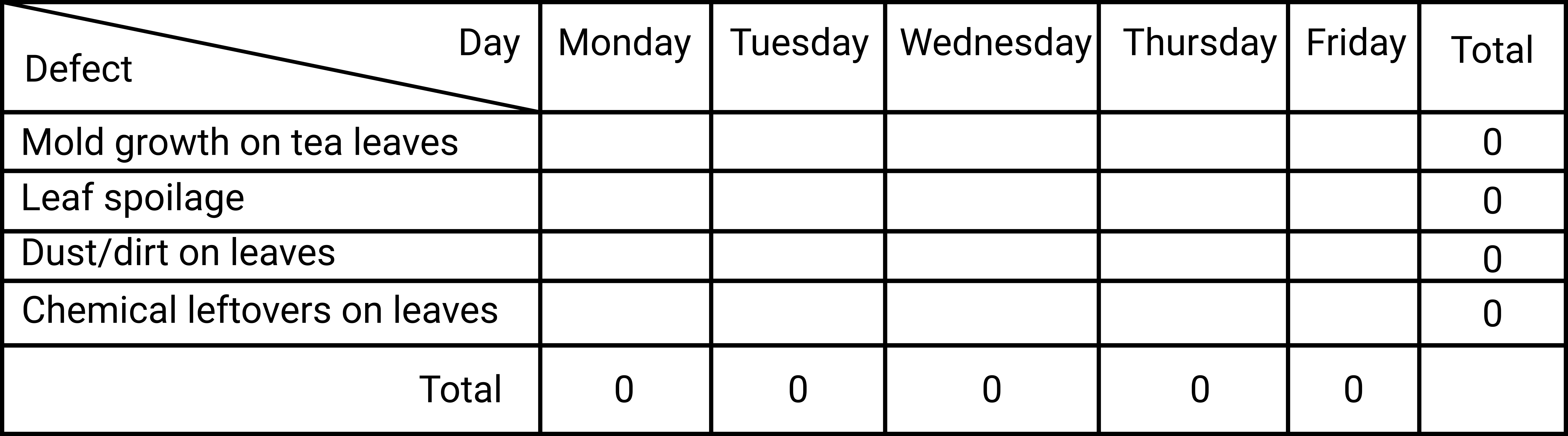
At the end of the week all that’s left is for us to cumulate the values for each day and each type of defect and there you have it; we now have a centralized and easy-to-visualize overview of the types of defects found in the production process every day of the week. This might be a good starting point to delve deeper into what’s happening in the production process. For instance, we might start to look into what is causing so many defects to appear on Wednesday. (Is the humidity in the facility different perhaps? or could the workers be more tired? Are we rushing to meet customer demands on this day? etc.) or the fact that so many defects are related to the dust/dirt on leaves might catch our eye (Is the cleaning process not thorough enough? Or is the environment itself dirty?)
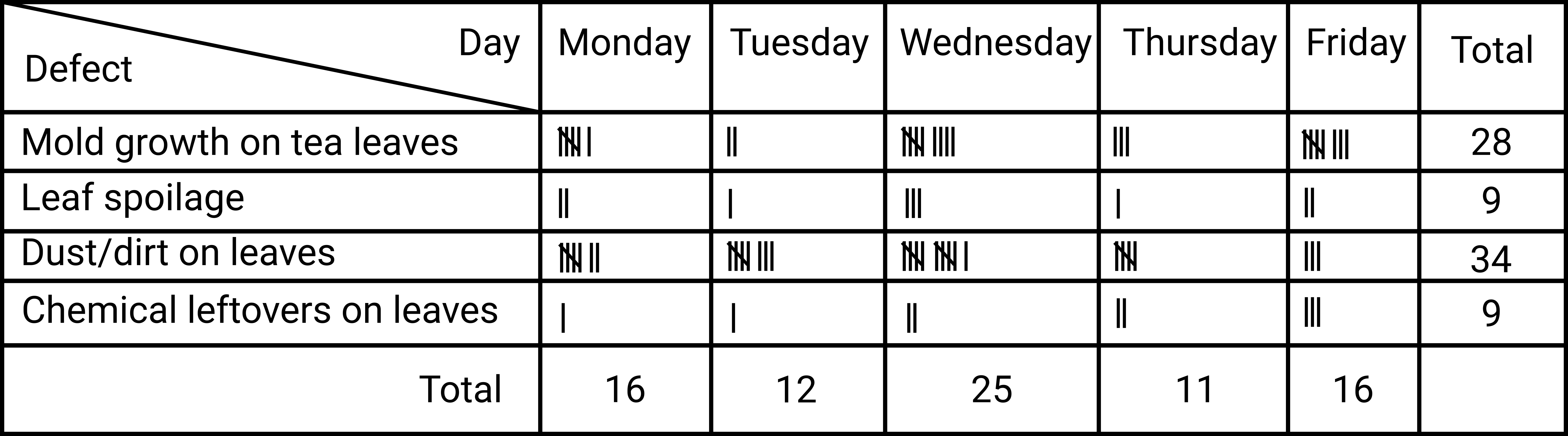
Now let’s try to think of a different example of how a check sheet might come in hand, still in the case of our fictional tea-making company. Let’s say that after talking to our employees we discovered that a lot of the defects are caused simply by employees forgetting to do some mundane tasks or skipping a step in the production process. To make it easier on them, we could create a flowchart of the process (read more about the flowchart here), but since we want an additional layer of protection against possible mistakes, we will use the info that we gathered and create a checklist for our workers. Unlike the check sheet which helps us observe and collect data, the checklist is a mistake-proofing tool that helps us easily spot if all the necessary steps have been taken.
Below we have an example of a checklist for our simplified tea production process, and in this case, we even added a column for employee comments.
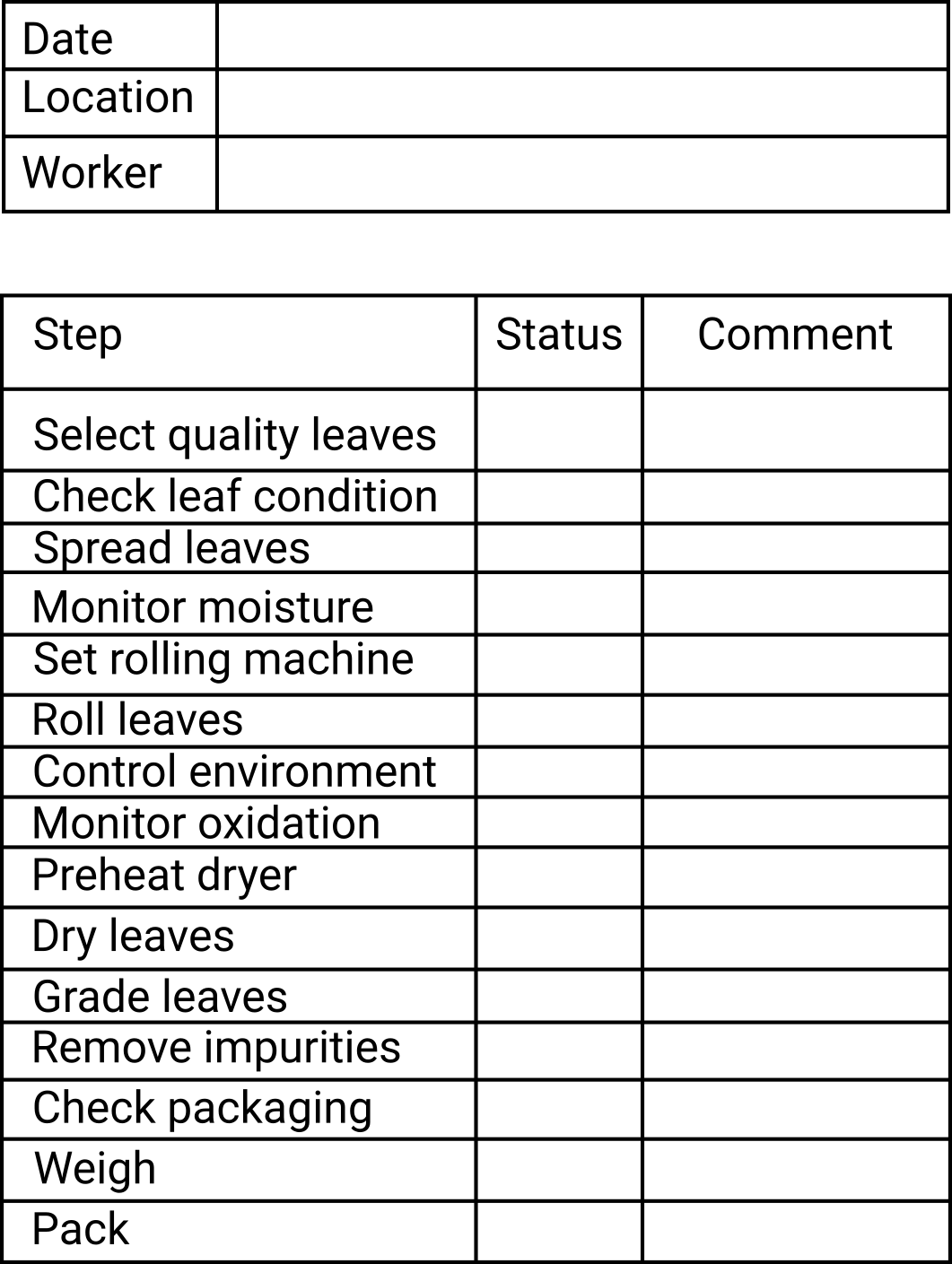
In case we are worried that workers might forget some key aspects of a step (say they might not remember that the moisture content must be between 3-5%), nobody can stop us from adding another column with additional instructions. And that’s the beauty of these tools, like many others, you can mold them to meet your requirements and use them in a way that is best suited for you. Here’s what that would look like for our example.
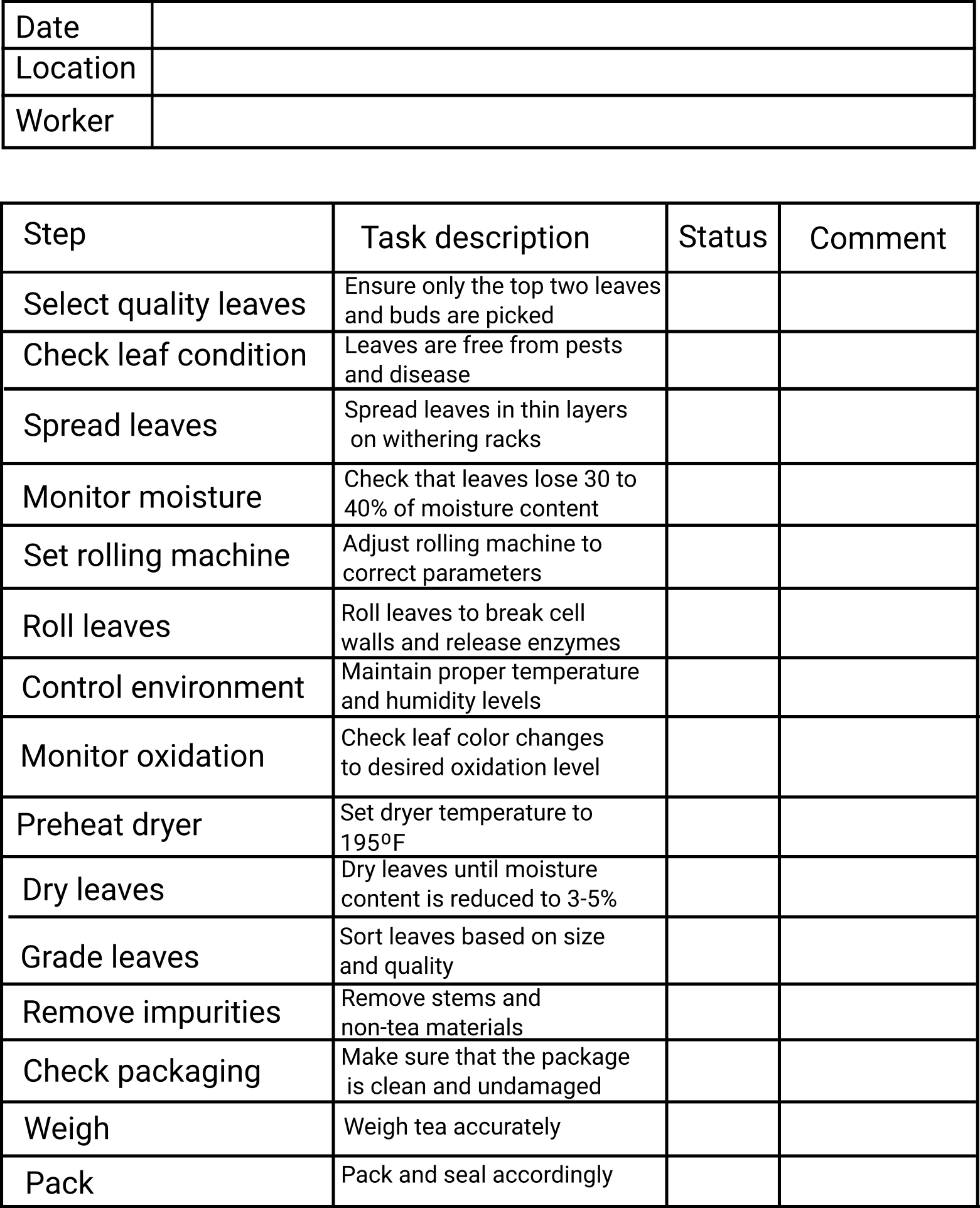
I hope these examples helped you gain the confidence you need to play around with these incredibly useful tools.
So as always, try it, learn from it, change it to your needs, and make it work for you. And if it simply doesn’t work, then drop it and don’t worry about it, there are plenty of other quality tools that can help you.
Leave a Reply